VMG Mixing Unit
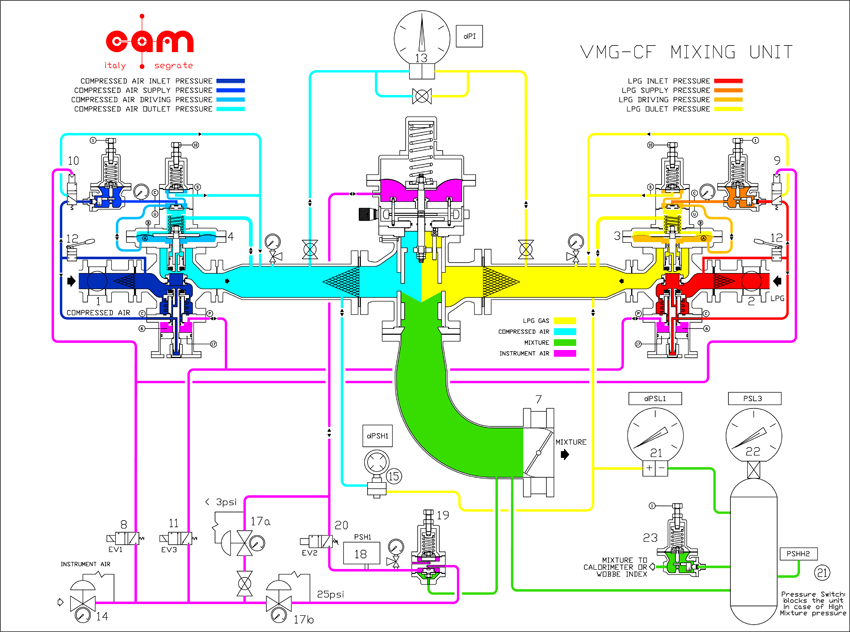
The mixing unit provides a variable flow-rate of LPG/Air mixture, according to the request (from 5% to 100% of its nominal capacity), with a steady output pressure. At the same time this unit is capable of maintaining a constant LPG/Air ratio on a value manually adjusted by the VMG valve. The automatic functioning of the unit is managed by a PLC installed in the Control Board. The mixing unit automatically starts and begins to deliver mixture, as soon as the downstream pressure drops due to the gas consumption of the users. When the pressure drops below the set point, the pneumatic servo control (pos. 19) raises its output signal, until it reached the set value of the pressure switch PSH1 (pos. 18), whose contact will be detected by the PLC. The Control Board activates the solenoid valve EV1 (pos. 8) and opens at the same time the two Pressure Regulators (gas and air - pos. 3 - 4). Following this, the pressure downstream the Regulators increases up to the set point value (about 0.3 bar above the set point of the VMG) and the differential pressure between LPG and Mixture raises until the opening of the contact of the pressure gauge dPSL1 (pos.21). A few seconds after the contact of dPSL1 has opened, the Control Board activates the solenoid valve EV2 (pos. 20), which was holding the VMG at minimum flowrate position. At this point the Valve starts to regulate the delivery of the mixture, in order to keep the pressure steady in the network. When the consumption drops below the minimum capacity of the VMG (about 5% of the flow-rate), the downstream pressure tends to rise while the differential pressure between LPG and Mixture decreases. As soon as it reaches the low limit and closes the contact of the pressure gauge dPSL1 (pos. 21), the Control Board stops the unit, by closing the solenoid valves (EV1 - EV2 pos. 8 – 20). The minimum of the Mixing Valve is set during manufacture by means a mechanical lock mounted inside and can be only increased by adjusting the signal through the Pressure Regulator (pos. 17a). Otherwise the line of this Regulator must be kept closed. When the consumption is lower than the minimum flow rate of the VMG , the differential pressure between LPG and Mixture does not reach the threshold of the dPSL1 pressure gauge and so the unit continues to operate ON / OFF at the minimum flow rate (with EV2 pos.18 always de-energized ).
VMG Valve
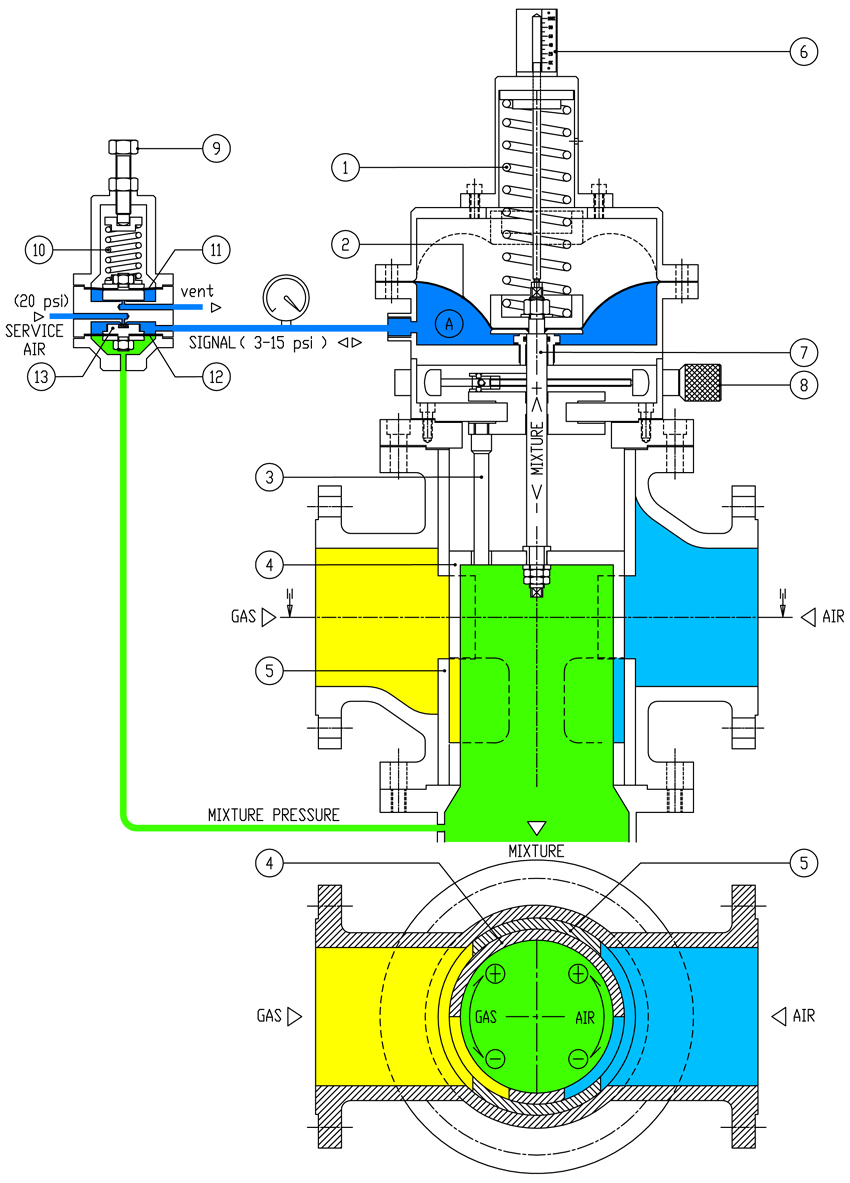
The mixer valve, “VMG-CF” series, is designed to deliver an Air/Gas mixture with a fixed ratio all over the range of flow rate (from 5% to 100%), keeping the downstream pressure steady. The gas/air mixing ratio can be adjusted through the hand-operated twist grip (8) in a range between 25% and 75% of gas in the mixture: the set value is shown by a sliding index placed on the valve body. The gas and air pressures at the valve inlet must be the same and 300 mbar higher than the required pressure of the mixture. The valve regulates the mixture flow rate by opening and closing the two ports where gas and air pass through. This is achieved by sliding the piston (4) inside the cylinder (5) where the ports are obtained. The piston is connected to the diaphragm (2) by means of the rod (7) and it is normally kept in closed position from the preload of the spring (1). It is driven by the service air pressure, into the chamber (A), which shall be about 15 psi for the complete opening of the ports. The pressure in the chamber (A) is continuously adjusted by a pneumatic servo control, according to the pressure of the mixture. So, for instance, when the pressure of the mixture tends to drop because of the consumption, the servo control increases the air pressure in the chamber in order to raise the flow rate and restore the set pressure. The pressure value of the mixture can be set by means of the adjusting screw (9), by turning it clockwise to increase or counterclockwise to decrease.
Lpg Pressure Regulator
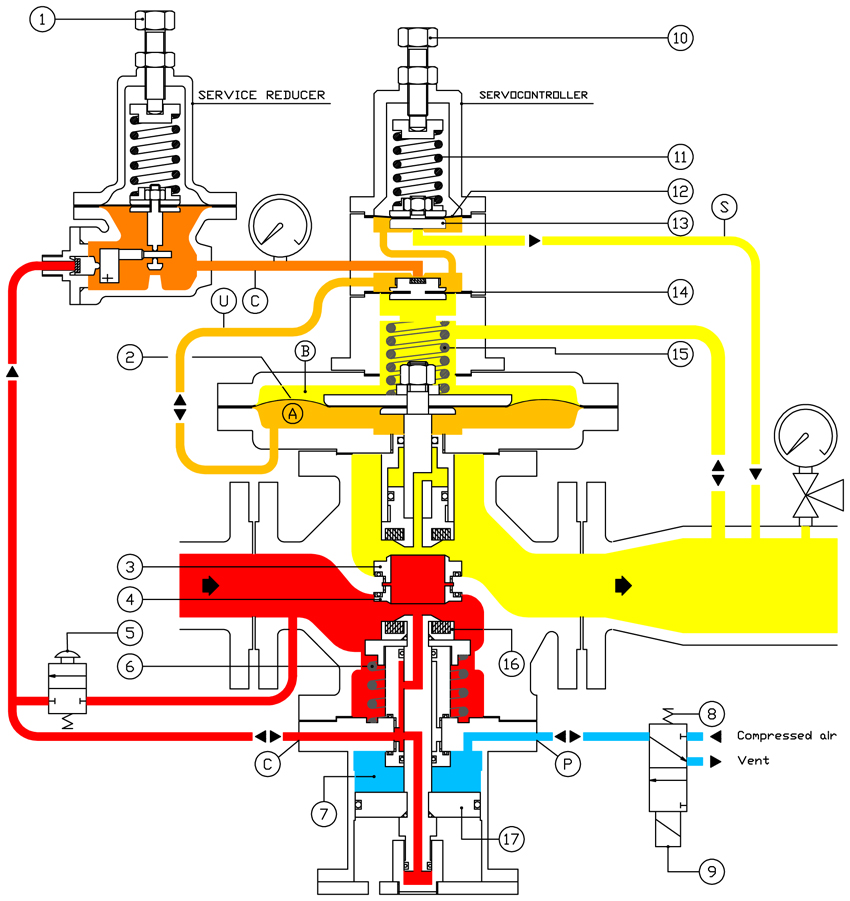
The seat (3) is normally kept closed by the spring preload (15). The seat (3) opening is due to the feeding of the service gas into the chamber (A). The service gas pressure for a complete opening of the seat must be at least 300 mbar higher than the pressure reducer setting value. Service gas pressure is controlled by the servocontroller provided with an inlet (C) and outlet (S) port. The ports opening is regulated by the shift of the servocontroller mobile equipment (13) connected to the membranes (12-14). The inlet port (C) is normally open because of the spring thrust (11) while the outlet port (S) remains closed. On the lower membrane (14) there is an uplift pressure created by the downstream pressure in chamber (B), this uplift is opposed to the spring thrust (11). Until the pressure on the lower membrane (14) is less then the spring thrust (11), the service gas, which feeds the chamber (A), opens the seat (3) and therefore causes the increase of the downstream pressure. When this pressure reaches the value to balance the spring thrust (11), (setting value), the mobile equipment of the servocontroller shifts in order to keep the pressure arisen in the chamber (A) at a constant level. If the regulated pressure (downstream the reducer) tends to overcome the setting value, the servocontroller mobile equipment (13) shifts upwards in order to reduce the pressure in chamber (A), blowing off the service gas through the outlet port (S), so reducing the openings section of the seat (3) until pressure downstream reaches the setting pressure. The setting pressure value can be changed by using the adjusting screw (10), turning the screw clockwise to increase it and counterclockwise to reduce it. The safety stop valve, incorporated in the reducer, works with gas or compressed air operated feeding. The stopper (16) keeps the bottom of the seat (4) normally closed, because of the spring preload (6). The opening of the seat (4) is done by the air pressure into the port (P). When the pressure downstream reaches the setting of the electrical switch, the EV valve change its position by the spring (8), and vents the air. The stopper is no more kept, so that the uplift of the spring (6), makes it move up and close the seat (4).
Air Pressure Regulator
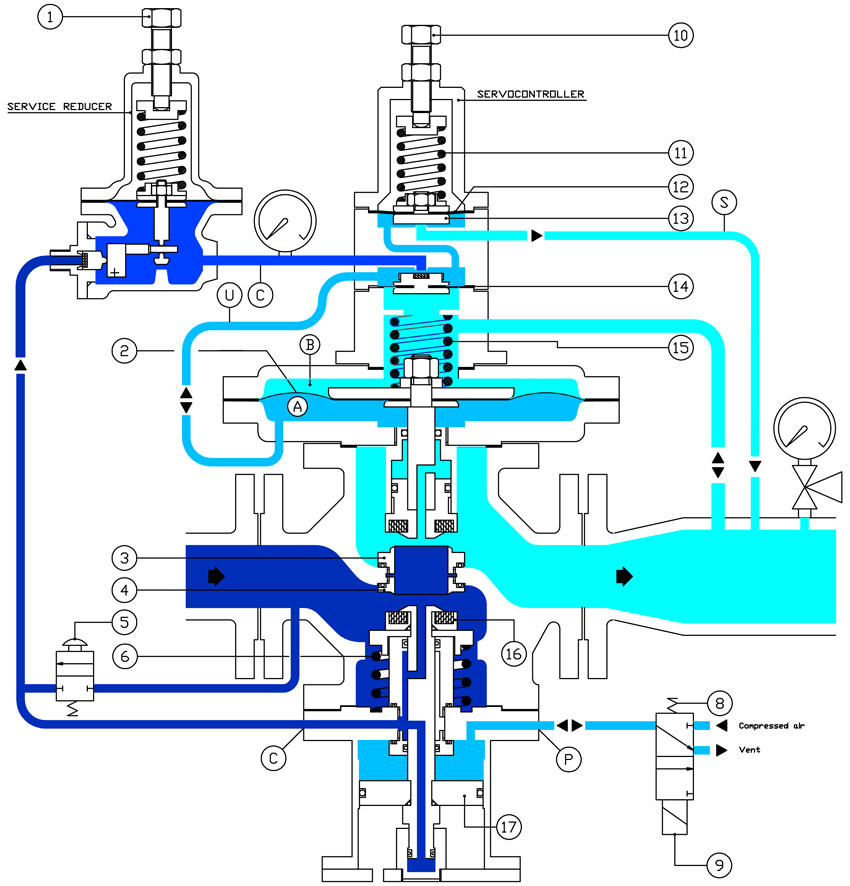
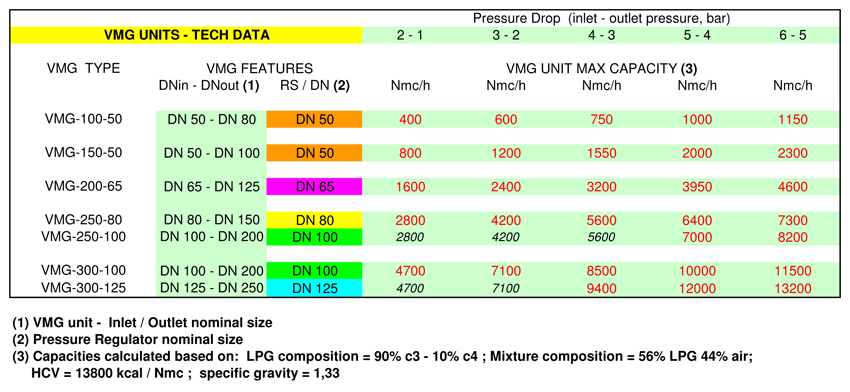